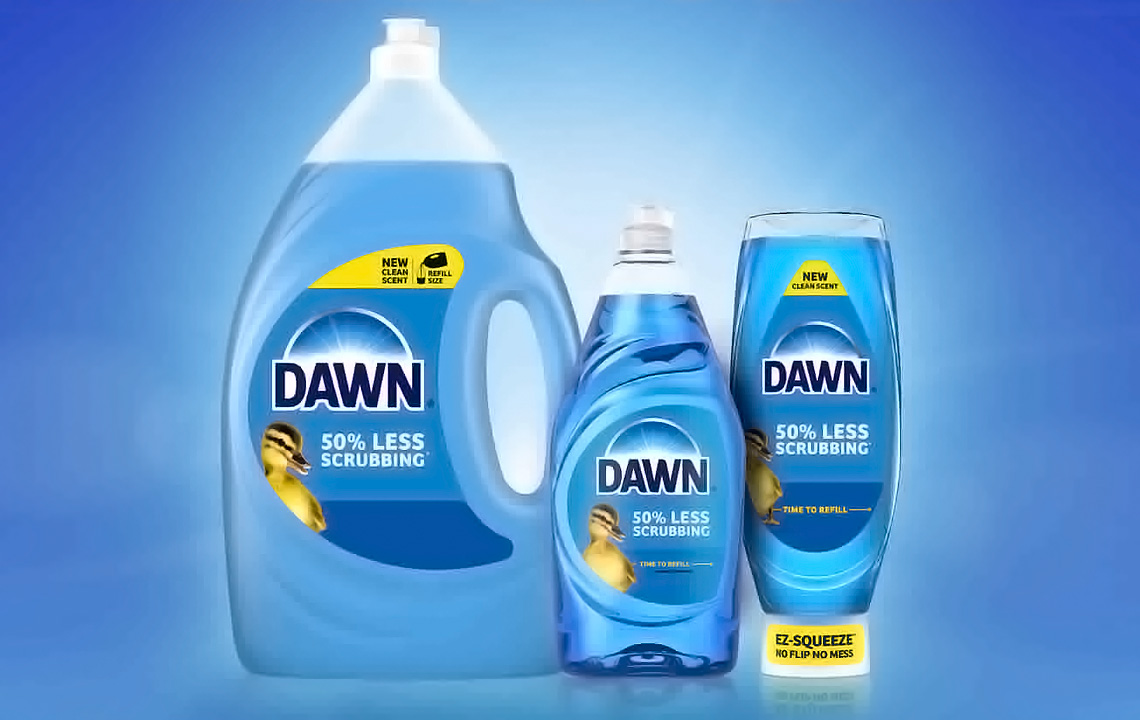
Most dishwashing liquids are septic/aerobic safe if used in reasonable amounts. Dawn dish soap is generally considered safe for septic systems. The key factors that make Dawn and similar dish soaps septic-safe include their biodegradability and low impact on the balance of bacteria in septic tanks.
Safe and Effective
Dawn dish soap is known for its effectiveness in cutting through grease and grime on dishes. While it is tough on grease, it is also designed to be gentle on the environment. The formula is biodegradable, which means it can break down into natural substances over time. This is crucial for septic systems as they rely on the natural breakdown of waste to function properly.
Safe for Bacteria
In septic systems, bacteria play a crucial role in breaking down solid waste. Harsh chemicals can disrupt the balance of these bacteria, potentially leading to septic tank issues. Dawn dish soap, being a mild and biodegradable detergent, is less likely to harm the beneficial bacteria in septic systems.
A Septic-safe Product
It’s important to use household products that are septic-safe to ensure the longevity and proper functioning of the septic system. Septic-safe products, like Dawn dish soap, are formulated to be compatible with the sensitive environment of septic tanks.
Additionally, Dawn offers a variety of formulations, including some that are labeled specifically as septic-safe. While the regular Dawn dish soap is generally considered safe for septic systems, using a product that is explicitly labeled as septic-safe can provide additional peace of mind.
When using any dish soap in a septic system, it’s advisable to use it in moderation. Excessive use of any detergent, even if it’s septic-safe, can still impact the bacterial balance in the septic tank. Using the recommended amount for dishwashing tasks helps maintain a healthy septic system.
Why Septic-safe Matters
There are various reasons why dish soap can be detrimental to septic systems. It can disrupt the balance of bacteria which is crucial for the proper functioning of septic systems. This disruption can cause clogs and backups that can be expensive to fix. Dish soaps often contain harmful ingredients such as phosphates, synthetic fragrances, sulfates, and chlorine that can be damaging to septic systems. Sulfates that produce suds can kill the necessary bacteria in septic systems. Chlorine can also eradicate the bacteria in septic systems, resulting in clogs and backups. Choosing a dish soap without these harmful ingredients is crucial to maintaining the proper functioning of septic systems and protecting the environment.
Dawn has developed a reputation for being safe for septic systems. This reputation is largely due to the fact that Dawn does not contain phosphates, which can harm the environment and contribute to algal blooms. While Dawn contains sulfates, which can kill off the bacteria necessary for the septic system to function properly, the sulfates in Dawn are present in small enough quantities that they are unlikely to cause harm.
In conclusion, Dawn dish soap is safe for septic systems due to its biodegradable nature and mild formulation. Dawn’s effectiveness as a degreaser means that it can clean dishes with less soap than other brands, which can help to reduce the amount of soap that goes into the septic system. Additionally, Dawn contains enzymes that can actually help to break down organic matter in the septic system, which can be beneficial. Using septic-safe products is essential for preserving the health and functionality of septic tanks. Always follow recommended usage guidelines to ensure optimal performance and longevity of your septic system.