How Does a Backflow Preventer Work?
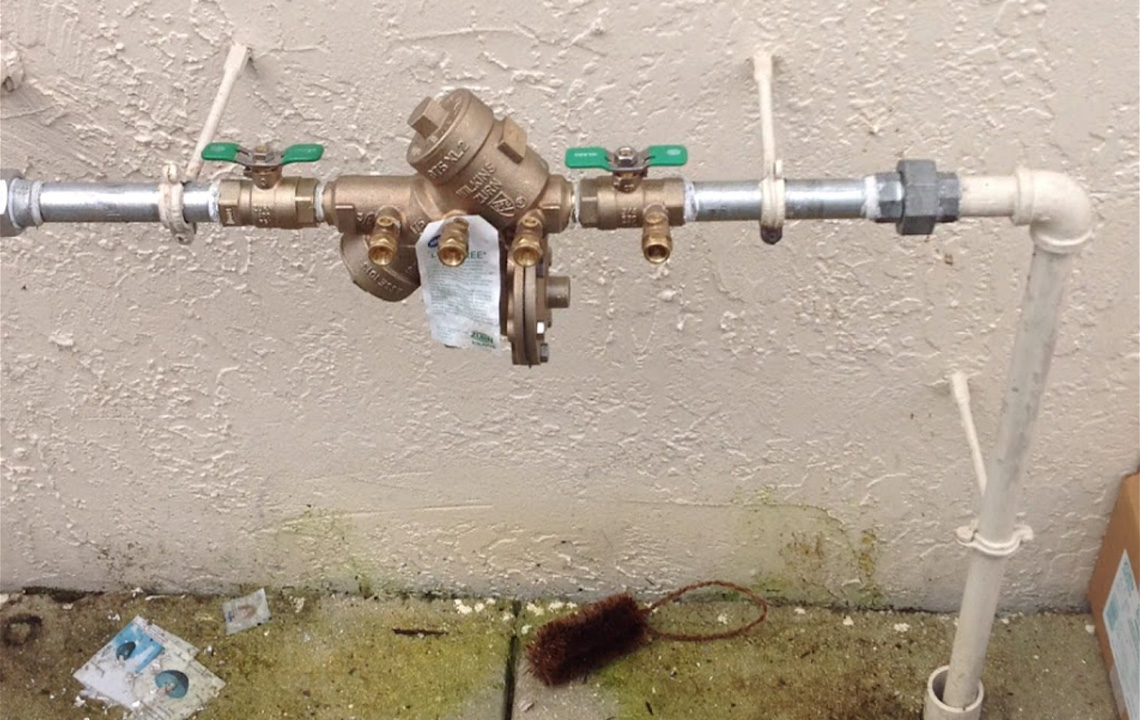
A backflow preventer is a crucial component of plumbing systems designed to ensure the safety of potable water by preventing the backward flow of contaminated water into clean water supplies. Understanding how a backflow preventer works requires insight into its various types, mechanisms, and applications.
Types of Backflow Preventers
- Air Gap: An air gap is the simplest form of backflow prevention. It involves creating a physical separation between the outlet of a plumbing fixture and the flood level rim of a receiving vessel. This ensures that there is no direct connection between the two, preventing backflow.
- Check Valve: A check valve, also known as a non-return valve, allows water to flow in only one direction. When water flows in the intended direction, the valve opens, but if there’s a reversal in flow, the valve closes, preventing backflow.
- Double Check Valve Assembly (DCVA): This consists of two check valves in series, along with isolation valves at each end and test cocks for verification. It provides a higher level of protection compared to a single check valve.
- Reduced Pressure Zone (RPZ) Assembly: RPZ assemblies provide the highest level of protection. They consist of two check valves separated by a relief valve. If the pressure between the two check valves drops below the supply pressure, the relief valve opens, releasing water and preventing contamination.
Mechanism of Operation
The operation of a backflow preventer depends on its type:
- Check Valve: When water flows in the correct direction, the pressure of the water pushes against the valve, causing it to open and allowing water to pass through. If the flow reverses, the pressure from the backflow closes the valve, preventing contaminated water from entering the clean water supply.
- DCVA: Similar to a check valve, the DCVA operates using two check valves. If one fails, the second acts as a backup. The test cocks allow for periodic testing to ensure proper functioning.
- RPZ Assembly: In an RPZ assembly, if the pressure between the two check valves drops, indicating a potential backflow situation, the relief valve opens, creating a low-pressure zone that prevents contamination.
Applications and Importance
Backflow preventers are critical in various settings, including residential, commercial, and industrial applications. They protect water supplies from contamination caused by back-siphonage or back pressure events. Back-siphonage occurs when there’s a sudden drop in supply pressure, such as during firefighting or water main breaks, while back pressure occurs when downstream pressure exceeds supply pressure due to factors like elevated tanks or pumps.
Maintenance and Testing
Regular maintenance and testing are essential to ensure the proper functioning of backflow preventers. This typically involves visual inspections, performance testing, and repairs or replacements as necessary. Qualified professionals should conduct these activities according to local regulations and industry standards. Backflow preventers play a vital role in safeguarding potable water supplies from contamination. They employ various mechanisms, such as check valves, double check valve assemblies, and reduced pressure zone assemblies, to prevent the backward flow of contaminated water. Regular maintenance and testing are crucial to ensure their effectiveness and compliance with regulatory requirements, ultimately contributing to the safety and integrity of water distribution systems.