How to Tell if Your Backflow Preventer Needs Repairs
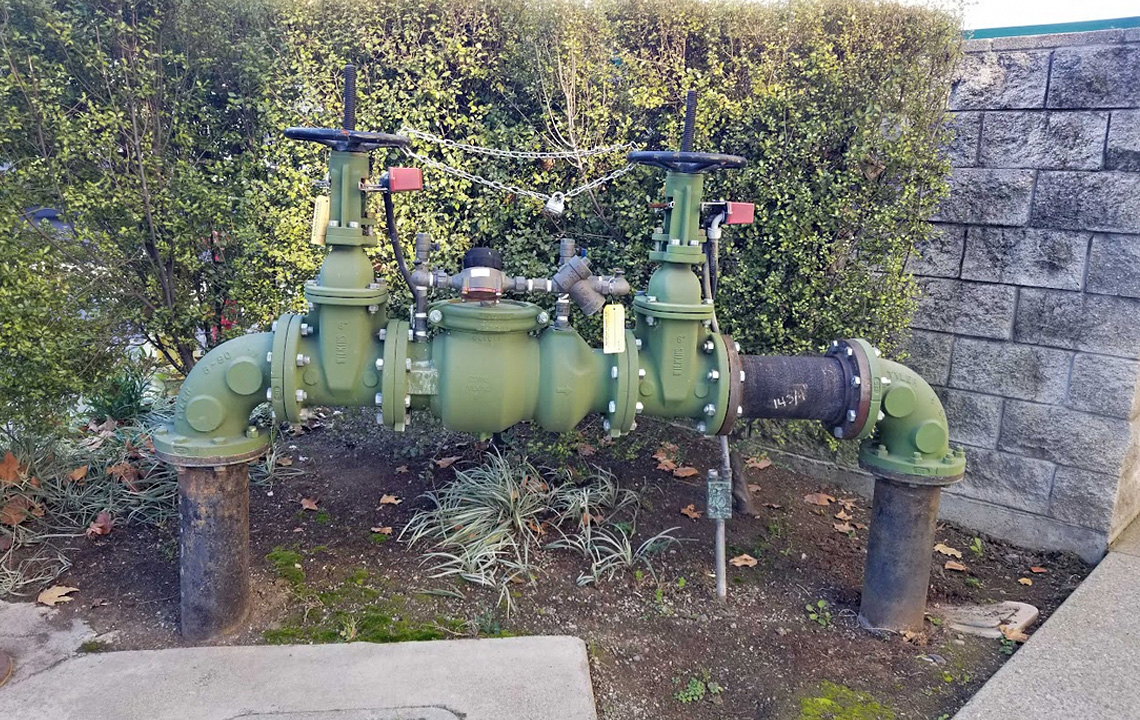
A backflow preventer is a critical component of plumbing systems, designed to prevent contaminated water from flowing backward and contaminating the potable water supply. Regular maintenance and inspection of backflow preventers are essential to ensure they function properly and protect public health. Here’s a guide on how to tell if your backflow preventer needs repairs:
Signs of Potential Backflow Preventer Issues:
- Visible Leaks or Drips: Inspect the backflow preventer for any visible leaks or drips. Leakage could indicate a damaged seal, valve, or other internal components.
- Reduced Water Pressure: A sudden decrease in water pressure throughout your plumbing system can indicate a malfunctioning backflow preventer. This reduction in pressure may result from blockages or valve issues within the preventer.
- Unusual Noises: If you notice strange noises such as hissing, gurgling, or banging coming from the backflow preventer or nearby pipes, it could indicate air pockets, debris, or water hammer issues within the device.
- Discolored Water: Water discoloration, particularly rusty or cloudy water, is a potential sign of backflow. If you notice any unusual coloration in your water supply, it’s crucial to investigate the cause promptly.
- Backflow Test Failure: Periodic testing of backflow preventers is required by many local regulations and standards. If your backflow preventer fails a routine test, it indicates a problem that needs to be addressed promptly.
- Corrosion or Rust: Check the backflow preventer for signs of corrosion, rust, or deterioration. Corrosion can weaken the structure and integrity of the preventer, leading to potential failure.
- Obstructions in Air Vents or Ports: Inspect the backflow preventer for any obstructions in the air vents or ports. Blockages can prevent the preventer from functioning correctly and may require cleaning or repairs.
- Inconsistent Valve Operation: Test the operation of the valves manually. If the valves do not open or close smoothly or if they stick in position, it could indicate internal damage or buildup within the preventer.
- Visible Damage: Look for any visible signs of physical damage, such as dents, cracks, or breaks in the casing or fittings. Even minor damage can compromise the effectiveness of the backflow preventer.
- Age of the Device: Consider the age of the backflow preventer. Like any mechanical device, backflow preventers have a lifespan and may require more frequent inspections and repairs as they age.
Steps to Address Backflow Preventer Issues:
- Schedule Professional Inspection: If you suspect any issues with your backflow preventer or if it has been more than a year since the last inspection, schedule a professional inspection. Certified plumbers or backflow prevention specialists can thoroughly assess the device and identify any problems.
- Perform Routine Maintenance: Regular maintenance is essential for the proper functioning of backflow preventers. Follow manufacturer guidelines and local regulations for maintenance schedules and procedures.
- Address Repairs Promptly: If any issues are identified during inspection or testing, address them promptly to prevent further damage or contamination risks. Repairs may involve replacing damaged components, cleaning internal parts, or adjusting valves.
- Replace if Necessary: In some cases, particularly if the backflow preventer is old or severely damaged, replacement may be the most cost-effective and practical solution. Consult with a professional to determine the best course of action.
- Keep Records: Maintain detailed records of inspections, tests, and repairs performed on the backflow preventer. This documentation is essential for compliance with regulations and standards and helps track the device’s performance over time.
By staying vigilant for signs of backflow preventer issues and taking prompt action to address any problems, you can help ensure the continued safety and reliability of your plumbing system. Regular maintenance and inspections are key to protecting the integrity of your water supply and preventing contamination incidents.